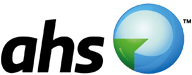
We've been delighted to welcome AHS on board as a new client of Pearson Electrical – a likeminded business striving, as we are, to continue servicing clients and their end customers despite the COVID-19 coronavirus pandemic.
The UK-based company supplied its state-of-the-art low ignition system air handling units for installation at the huge distribution centre of a major international online retailer near Magdeburg in Germany. The project required a contractor certified for working in explosive atmospheres (or ATEX rated) to complete a wiring project on the site’s air flow system because the area involved is used for storing aerosol products prior to them being dispatched. This impressive site comprises a three-level warehouse with pick towers, alongside office and welfare facilities catering for the 1,450 employees working there.
We were approached and, needless to say, were only too happy to help! We’ve now worked on four installations of AHS units and are looking forward to partnering up on more projects in the near future.
Specialist work
Jared Gray, Technical Director at AHS, said: “This is a highly specialist job involving explosive atmosphere wiring, and we were fortunate to find Pearson Electrical as not many companies have the required credentials or experience.
“We were really impressed by the Pearson team’s fast response, and the professionalism of the work done. Speed and flexibility were key drivers for us, and Pearson delivered on all counts.”
Mark Pearson, Owner of Pearson Electrical, said: “It’s our pleasure to work alongside a company that shares our commitment to the highest quality of work and professionalism. AHS supplies a range of air handling units primarily in the UK and is one of just a few such manufacturers based here, although some of its cutting-edge systems have travelled as far as New Zealand.
“Being NICEIC certified for ATEX work is something we are proud of at Pearson Electrical. It takes considerable investment in training to ensure our team remain up to date with this accreditation, but it’s rewarding work and means we can offer this scarce service to companies like AHS on some really exciting projects.”
As a smaller company, Pearson Electrical has the advantage of being able to respond very quickly to requests for this kind of work. “Bigger companies often have complex procurement systems to work through, which can take months,” Mark added. “Whereas I’m able to manage this process so efficiently that we are able to turn it around within a week.”
Great relationships at our core
We’d like to say a huge thank you to our clients, who are working proactively with us throughout the COVID-19 pandemic to help ensure the most positive outcome possible for our network of companies, staff and clients. It’s at time like these that the strong and positive relationships we are committed to building really come to the fore, and it’s by working together collaboratively in this way that we’ll thrive through the other side of this crisis.
How we can help your organisation
Our specific services include custom builds of LV switchboards, motor control centres, consoles, control panels and starters; control system design, build and installation; electrical testing and commissioning; primary and secondary current injection; portable appliance testing; 24-hour repair service and planned and reactive maintenance.
If you have an urgent electrical installation or repair you need our help with, you can contact us via support@pearson-electrical.com and 01482 225080 and we will aim to turn your job around to the highest quality, in the fastest possible timeframe. We can also help with mechanical motor breakdowns via our Humber Rewind armature winding sister company.
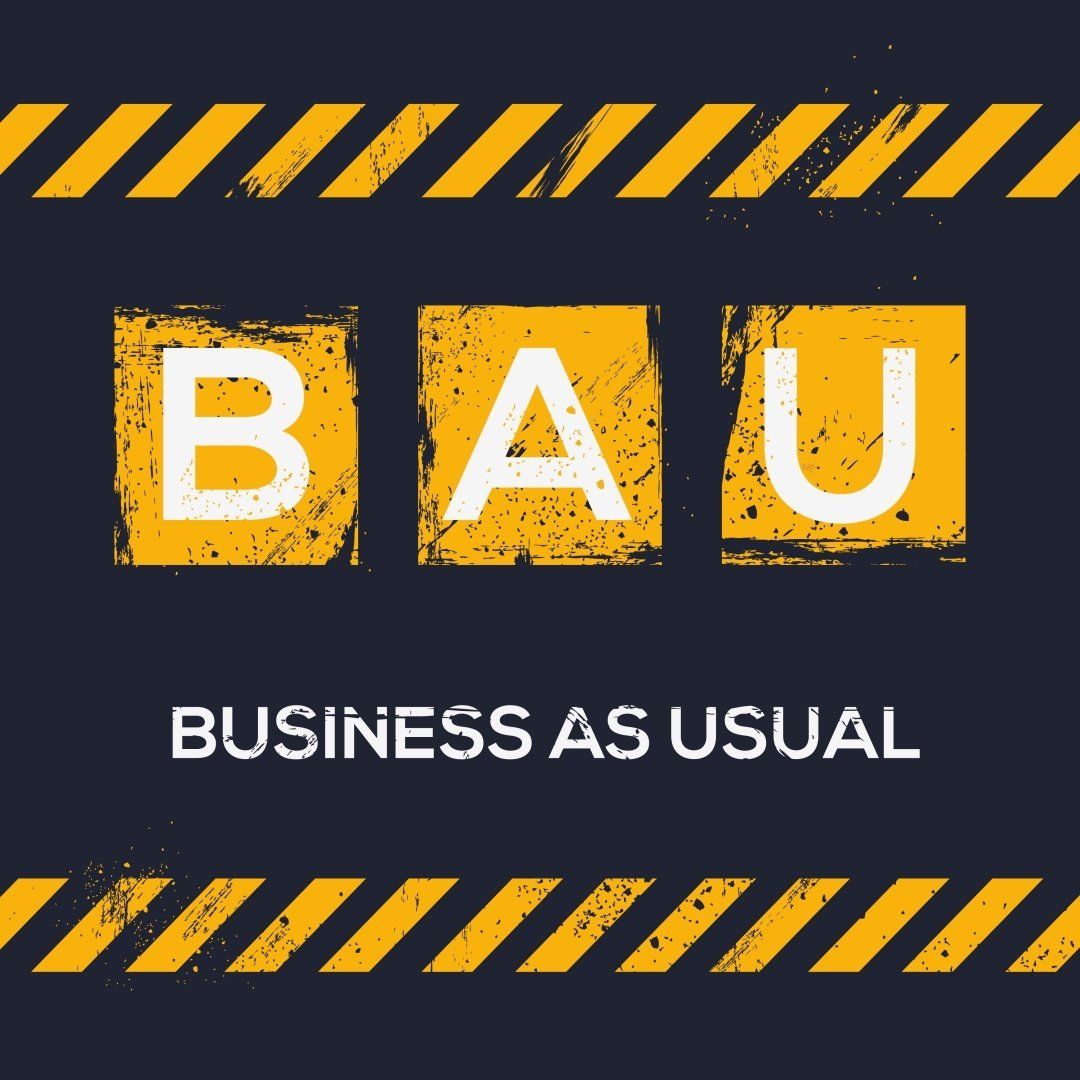